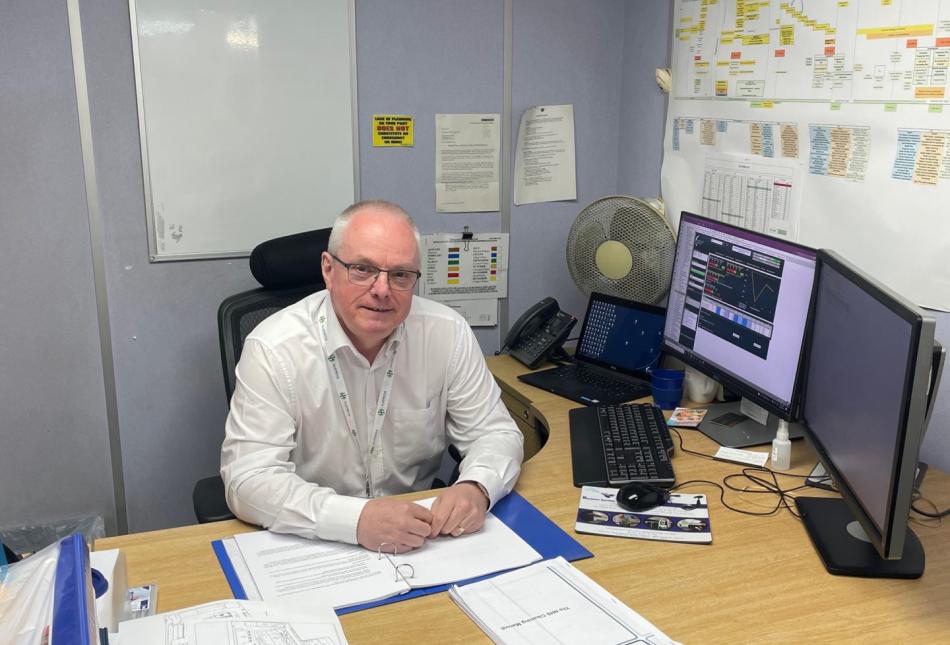
Portsmouth Aviation prides itself on providing high-quality products and services that have been tried, tested and delivered to our customers’ specific needs and requirements. We have a large team of quality engineers and technicians who are all highly experienced and are responsible for ensuring that each product is quality audited and approved.
Pete Vaughan, our Quality Manager has worked at Portsmouth Aviation since 1985. Pete is in charge of ensuring that we deliver all of our products and services on time and to a high standard.
What’s your career background?
After leaving Portsmouth Technical High School for Boys at the age of 16, I began working for The Metal Box Co. Ltd. between 1974 to 1978 as a Mechanical Engineering (Toolmaking) Apprentice, working in the toolroom and the Project Engineering Department. After qualifying, I took up the role of Mechanical Engineering Fitter under the Plastic Group Engineering Department, working alongside the design department to develop and manufacture machinery related to the plastic bottle moulding industry. During this period, I gained experience in the manufacture of components and the operation of a wide range of engineering machinery, culminating in the final assembly, testing and commissioning of equipment prior to delivery.
Sadly in 1985, I was made redundant from Metal Box due to them relocating. However shortly after being made redundant I joined Portsmouth Aviation Ltd. as a Quality Examiner. I was responsible for mechanical inspection and surveys of company products, across all areas of the company; fitting, press shop, welding, painting, metal treatments/plating, goods receiving and despatch areas of the company. I was also in charge of ensuring compliance to relevant drawing and specification requirements using the full range of manual inspection equipment.
In 1994 I was promoted to Quality Assurance Engineer at Portsmouth Aviation and became responsible for analysing and reporting the quality issue findings, controlling the internal auditing team which was made up of 15 team members and conducting internal audits. My duties also included maintaining quality records, conducting quality training and developing company quality procedures.
Since May 2002, I have been the Quality Manager, reporting directly to the Managing Director.
What does your role as Quality Manager involve?
Day-to-day, I manage the Quality Department and the range of activities undertaken by the Quality Engineers, Quality Technicians, Laboratory Technicians, Test and Calibration Technicians to ensure that the requirements are met for each product and service and ensure that the Production department is fully supported. I analyse Portsmouth Aviation’s delivery times and quality to ensure that our “right-first-time” performance is maintained in line with the company’s SC21 Silver Award status requirements.
As Quality Manager, I report the analysis results to the senior management team during our weekly Tier 4 meetings and our quarterly Management Review meetings. I conduct the quality review of the tenders and contracts coming into the company whilst managing the auditing system.
Finally, I ensure that all non-conformances raised are recorded and investigated in order to determine the root cause and establish the required containment, correction and corrective actions are applied in a timely and effective manner.
What are the most interesting parts of your role?
I would have to say the fact that every day presents a new challenge. As the company covers a huge range of engineering disciplines, there is always a new challenge that needs to be addressed. I would also say the close liaison with colleagues across the organisation; the ability to identify and develop solutions with team members is very rewarding.
What challenges do you face within your role?
The main challenges I face as a Quality Manager at Portsmouth Aviation are the limitations of some resources ie. team shortages due to sickness or COVID isolation – making it sometimes challenging to complete projects in very short time frames. The Quality Department mostly relies on a team of specialised workers in a wide range of roles and disciplines, these roles are often difficult to cover or replace within a short period of time due to their specialised nature and skill level.
Why is Portsmouth Aviation a great place to work?
At Portsmouth Aviation there is a wide range of processes and activities and types of work, meaning there are always new things to learn and new challenges to overcome. Portsmouth Aviation always maintains its values to ensure the company grows and develops in an ethically, environmentally and safe way. We have an open-door policy, meaning I have easy access to discuss anything with the team at all levels; from the Managing Director to the team on the shop floor. It is run with a friendly family atmosphere, everyone is always treated as part of the Portsmouth Aviation team – it’s great to all be working together to achieve the common goal.
If you’d like to learn more about the work we do within our Quality Department or if you have an interest in starting a career with Portsmouth Aviation, please get in touch.