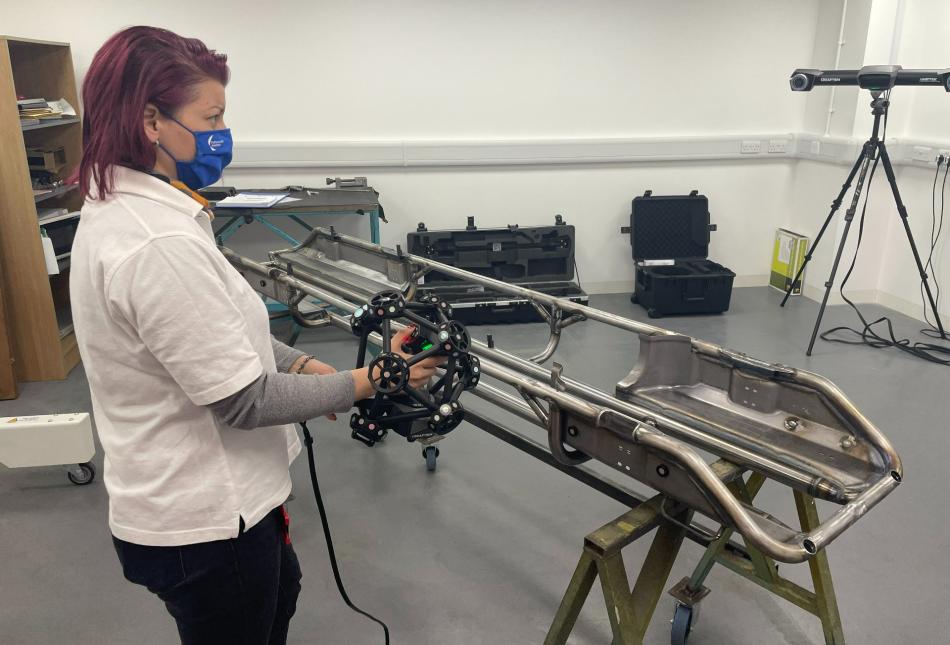
At Portsmouth Aviation we are never dormant to change and are always looking at ways to reshape our processes to accommodate new exciting technologies. With the Covid-19 pandemic causing global disruption to supply chains, it was clear that changes were needed to combat staff shortages and reduce timely processes.
As a reactive business that has continued to thrive in these unprecedented times, we introduced the further use of 3D scanning technology in the form of a portable Coordinate Measuring Machine (CMM) by Creaform – complete with HandyPROBE Next™ and MetraSCAN3D. It has one of the fastest scanning capabilities currently available on the market, and has made a dramatic difference in saving our resources and streamlining our processes.
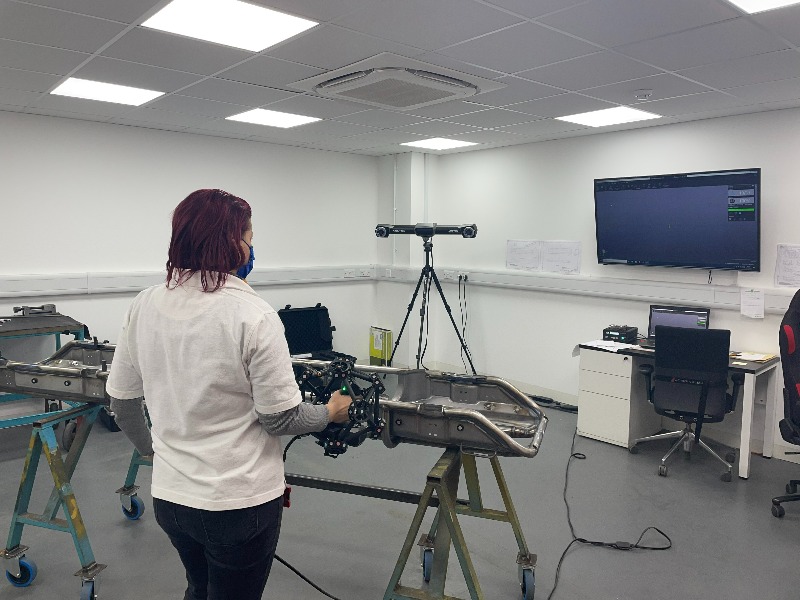
How 3D scanning is used in manufacturing
Scanning is an important part of the design and manufacturing process. 3D scanning has continued to innovate the manufacturing world for decades. Since its creation way back in the 1960s, it has silently developed to shake the traditional manufacturing methods. The function itself, brings convenient usage to supply chains in an ever-growing range of industries; from automotive to movie production.
It is a contraption that uses non-contact laser light to capture the precision points of a 3D object. It enables the digital capture of fine details, free form shapes, and measurement of complex geometries. The data capture is often referenced as a point cloud and displays the precise points of the object together in a digital file.
How portable scanning differs from traditional fixed CMM use
The Creaform CMM that is now a tool in our supply chain, is a portable solution that offers simplicity in our quality assurance process. It can test different parts of products during the design and manufacturing process, against the intent and specifications of our designs. The biggest difference we have seen between this and a more traditional fixed CMM, is the flexibility in its use. The combination of the HandyPROBE Next™ and MetraSCAN3D is completely unrivalled, offering the simplicity of a traditional measuring arm without the limitation of a fixed setup. We can simply take the portable CMM to the part we want to scan, instead of having to set a part up on a fixed position machine, meaning we can use it directly on the shop floor.
The HandyPROBE Next™ is a lightweight, wireless handheld probe that measures points on a part using a standard probe stylus. The handheld probe is tracked in real-time by the C-Track optical tracker, providing a precise coordinate location of the probe tip at all times. Compared to traditional CMM use, the technology provides even further measurement accuracy that is insensitive to the instabilities of any environment. We have found this to be an impressive feature that allows us to get close to the part we are measuring as possible with no issues. There is no loss in accuracy, or need to perform cumbersome manoeuvres, so any accidental movement or the effects of vibrations are completely eliminated.
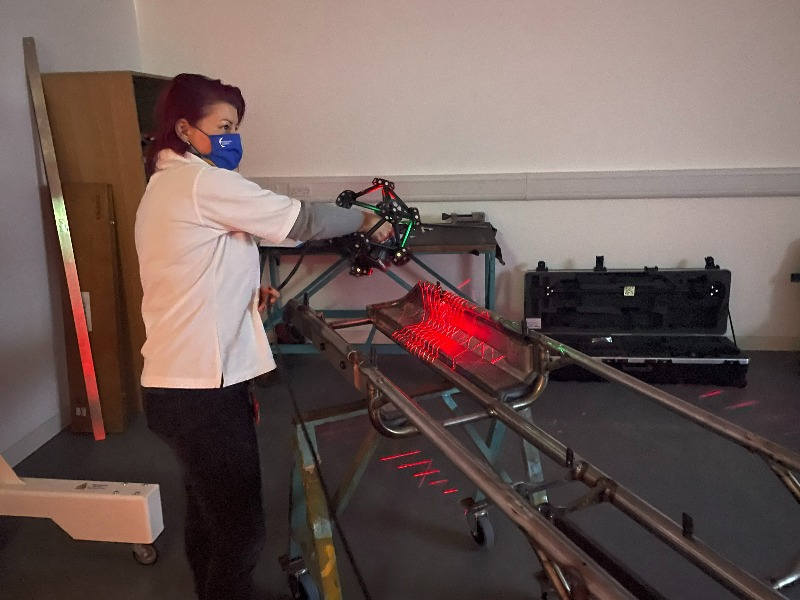
Product design improvements
Being true to our mission statement, the portable CMM has advanced and reshaped our design process. New technologies, techniques, and processes allow us to be efficient and cost-effective. Digital design models play a crucial role in component design and analysis to inform our decision making, and our new CMM has elevated that for us even further.
Something we find most impressive and exciting about our new product design tool is the ease of reverse manufacturing. Reverse manufacturing allows us to take a finished product, no matter how new or old, and scan it to use as a reference for new CAD designs. This works by using the portable CMM to digitise the existing part or object, so that we can use it in our CAD software, SOLIDWORKS. We can then use this as the basis for new designs and product development.
Streamlined quality assurance
As well as transforming our product design workflows, our quality assurance process can also reap the benefits of the portable CMM. We can complete a full dimensional analysis with accuracy like never before, supporting our engineering analysis team in their quality validation. The quality department can now complete inspections and analysis on the shop floor with ease. Our team can scan various part sizes and surface finishes, getting as close to the part as possible. This dramatically simplifies the operation, giving us the ability to measure objects of all sizes with wider movement capabilities at a fraction of the cost and time of a comparable laser tracker. Dynamic referencing, automatic alignment, and continuous monitoring of parameters are a particularly impactful benefit; attributed to the optical tracking camera, C-Track.
Our quality team can use the data captured by the portable CMM to measure individual parts in comparison with the original CAD data. This prevents production errors because we can assess the alignment of the parts and any variation in their positioning; correcting imperfections or potential design changes prior to parts being sent for production. Engineering CAD is key to our technical services offering, so our in-house design team now has even more assurance that our products and engineering solutions meet the precise requirements and specifications of all of our clients.
If you’d like to learn more about the services we offer and the work we do, please get in touch.