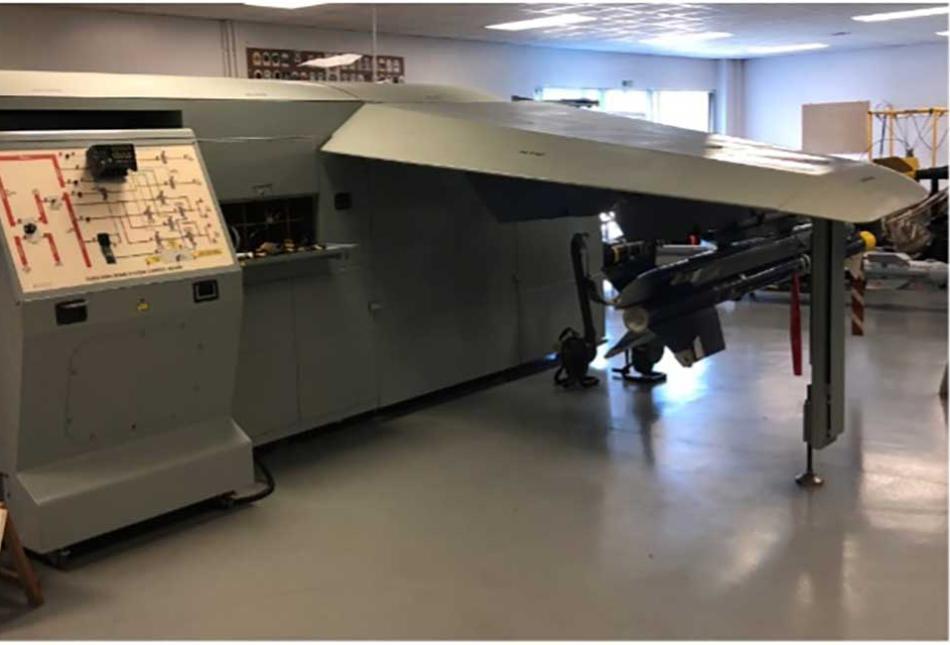
The Design & Manufacture process was overseen by a Project Manager to ensure that the customer requirements were understood, achievable and complied with. The PM also ensured that the product was delivered to time and budget, quite a challenge during a worldwide pandemic.
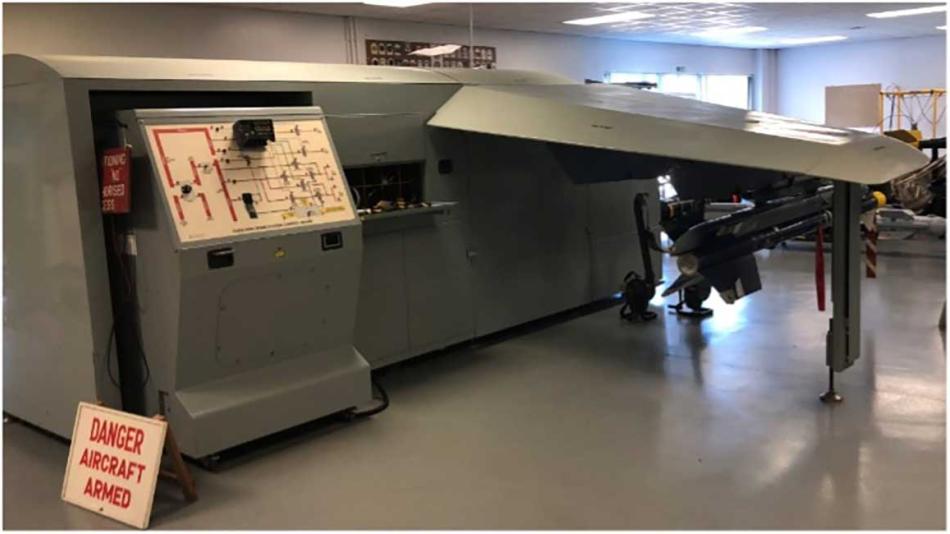
Portsmouth Aviation and Pennant International
Pennant International became aware of Portsmouth Aviation’s comprehensive engineering and design capabilities and approached us to determine if we were able to support them in updating a product that they had previously supplied in the 1970s. Sketches and photographs were available, but the design was otherwise starting as a blank piece of paper.
CADMID and FEA
Our engineering and design experts with weapon loading experience, worked with Pennant to establish what was achievable and compile a technical requirement specification. We then undertook a design process in line with our Design Approved Organisation Scheme (DAOS) status which also included following the principles of CADMID. This process incorporated CAD design alongside stress analysis (Finite Element Analysis – FEA), to ensure the unit met structural strength requirements due to the significant masses that were to be suspended from the unit.
Given the weapons trainer is to be used in a training environment, it was critical that safety factors were fully appreciated through the development. A full suite of Hazard Identification & Safety Management activities were undertaken by our in-house Safety Engineering team.
The design process was supported by passing through the Portsmouth Aviation Ltd Design for Manufacture (DfM) process to ensure manufacturing was aligned to our operational capabilities. Once approved by the customer, the drawing pack was passed to the Production and Operations Teams.
Parts were fabricated and machined using our extensive manufacturing facilities and the Quality Management team undertook First Article Inspections in line with our ISO 9001, rev D accreditation. Prior FEA conducted by our Stress and Aerodynamics Team was validated through load testing using our in house test capability.
NADCAP Approved Metal Finishing and Treatments
Our state of the art- and in-house NADCAP approved metal finishing and treatments capability, and our skilled fitters ensured the build was completed ‘under one roof’ and within project timescales. The construction culminated in a Factory Acceptance Test to present the unit to the customer and prove the processes detailed in the operation manual compiled to recognised technical documentation standards.
Benefits For Customers of Portsmouth Aviation Ltd.
Portsmouth Aviation were instrumental in supporting the WLT supplier, Pennant International Group Plc, in the design and manufacture of the trainer. The product allows safe classroom training of inert stores loading at both Fixed & Rotary Wing stations.
A wide range of company capabilities including SME knowledge, Design, Machining, Fabrication, Treatment and Painting, came together to deliver to schedule despite challenges presented by the pandemic.
Due to this success and customer satisfaction, Portsmouth Aviation Ltd are anticipating further orders, via Pennant, in the very near future.
For further information on this product and more please contact:
- Portsmouth Aviation Ltd – customerservices@portav.com
- Stuart Hooker at Pennant
- or visit: https://www.portav.com/ or https://www.pennantplc.co.uk/